Casting vs. Forging Aluminum Alloy Wheels – Test Your Vision
With the passage of time, more and more people are becoming aware of and accepting the many advantages of aluminum alloy wheels, leading to an increase in their use. But what is the difference between cast aluminum alloy wheels and forged aluminum alloy wheels?
1.Casting wheel production is relatively simple, suitable for mass production, and has lower costs.
Low-pressure casting is the most basic method for producing aluminum wheels, which is relatively economical. The most common methods are low pressure casting and high pressure mold casting. Low-pressure casting involves pouring molten metal into a mold to form a blank that is then hardened, cooled, and finally finished through a lathe and polishing process to obtain the finished product.
High pressure casting is a more advanced casting method that uses the suction generated by high vacuum to suck molten metal into the mold. This helps maintain a constant temperature and eliminate impurities, resulting in castings without pores and with uniform density and higher strength than low pressure casting. The casting process is relatively simple, suitable for mass production, and helps reduce costs.
2.Forging wheel production is complex, more expensive, but has better performance.
Forging is currently the most advanced method for manufacturing aluminum wheels. Forged aluminum alloy wheels are produced by repeatedly forging a piece of aluminum ingot under pressure using a large forging press machine. After forging, the blank is then subjected to spinning treatment to extend the width of the wheel to meet the corresponding standards. After the spinning process, the wheel is almost formed and then undergoes precision machining, polishing, and painting to obtain the finished product.
Because the forging process is complex and the forging equipment is expensive (a large forging press machine can cost tens of millions of yuan), the cost of forging aluminum alloy wheels is relatively higher.
3. Metallographic analysis shows that forged wheels have better performance.
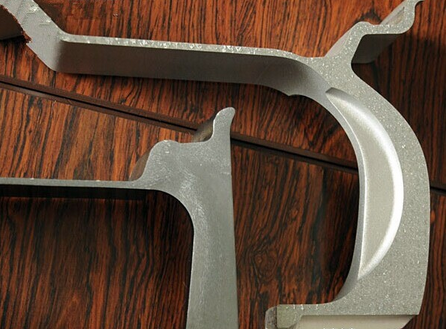
forged wheels Vs cast wheels
The cross-section of forged wheel is smooth (left) while the cast wheel has a rough texture (right).
In the image above, we can see that the cross section of the forged wheel on the bottom is very smooth, with tightly arranged metal grains and no rough feeling, while the metal grains in the cast aluminum alloy wheel are loose and the metal particles are larger, resulting in a very strong rough feeling on the cross section.
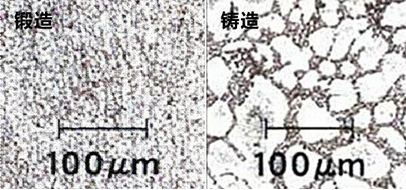
metal molecules of forged wheels VS metal molecules of cast wheels VS
Under microscope observation (as shown in the figure below), the metal molecules of the cast wheel hub have loose arrangement and larger particles, while the metal molecules of the forged aluminum alloy wheel hub are arranged very tightly. The tighter the arrangement of metal molecules, the higher the toughness, impact resistance, strength, and bearing capacity of the wheel hub.
Fourth, it is difficult to distinguish the appearance of forged and cast wheel hubs, only with significant differences in metal properties.
The toughness, impact resistance, strength, and bearing capacity of the forged wheel hub are higher than those of the cast wheel hub, while there is no significant difference in heat dissipation performance between the two. However, cast wheel hubs are generally about 20% heavier than forged wheel hubs.
In conclusion, although there are some differences between cast and forged aluminum alloy wheel hubs, the performance of cast alloy wheel hubs produced with the latest technology is already close to that of forged wheel hubs. Car enthusiasts can choose the appropriate aluminum alloy wheel hub according to their vehicle conditions, but beware of cast wheel hubs impersonating forged wheel hubs.