Advantages of Magnesium Alloy for Hub Processing: What are the Manufacturing Processes for Magnesium Alloy?
Automobile hubs, also known as wheel rims, are important components of vehicles. They are mounted on the axle, with the outer contour located inside the tire to support the vehicle’s tires. During the vehicle’s operation, it inevitably generates lateral loads, longitudinal loads, driving torque, braking torque, etc., and the hub needs to bear a significant portion of these loads.

forged Magnesium (6)
With the rapid development of the automotive industry, the materials used in automobiles are also moving towards high performance, multi-functionality, lightweight, and environmental friendliness. Light weighting of automobiles has become a global trend in automotive development. Light weighting refers to the reduction of the vehicle’s weight as much as possible while ensuring its strength and safety performance, thereby improving its power performance, reducing fuel consumption, and lowering exhaust emissions. In the process of automobile lightweight design, especially in the design and manufacturing of hubs, aluminum alloys, magnesium alloys, and titanium alloys have played a very important substitute role. As a new type of material for manufacturing automotive hubs, what are the advantages of processing magnesium alloy hubs? Let’s take a look at the five major advantages of processing magnesium alloy hubs and the manufacturing processes for magnesium alloy.
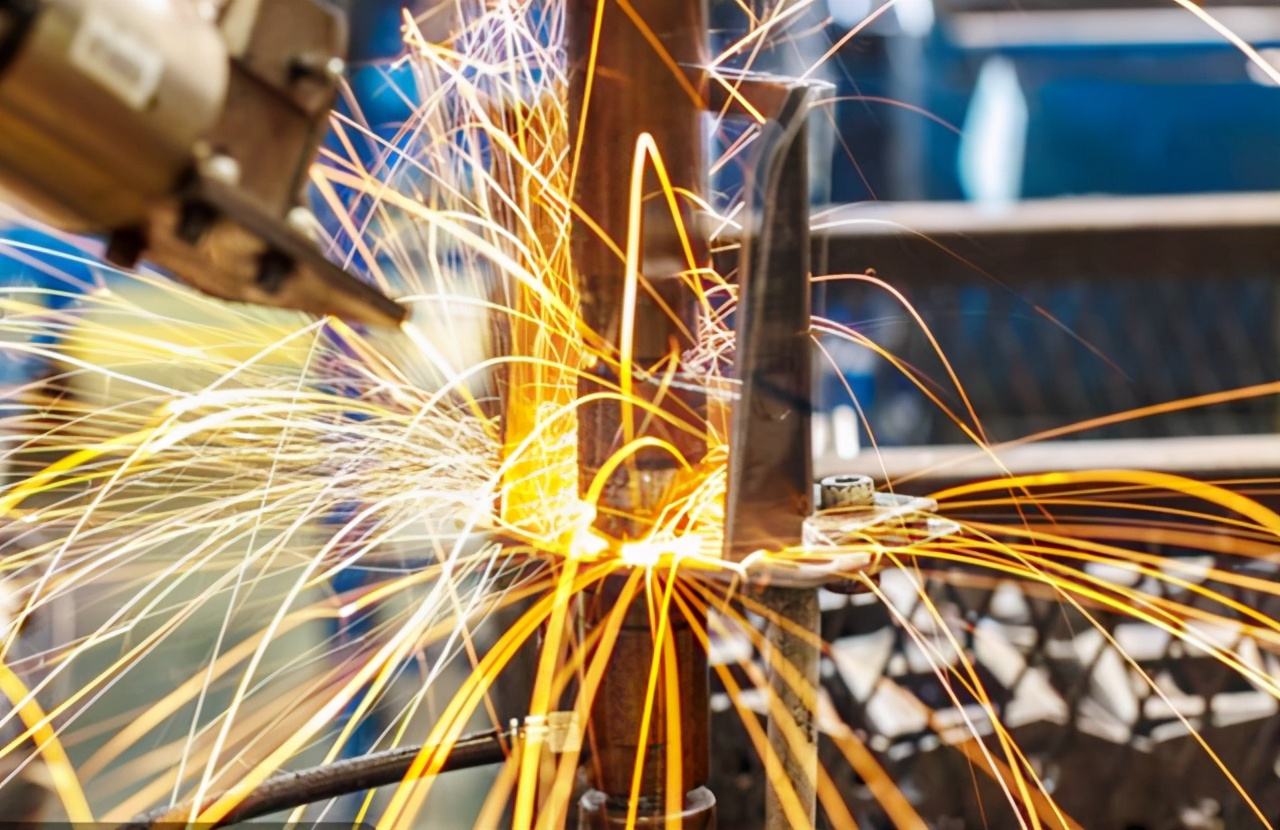
forged Magnesium (11)
I. Five major advantages of using magnesium alloy for hub processing:
-
Improved comfort with the use of magnesium alloy hubs:
Magnesium alloy hubs have the characteristics of absorbing vibrations and rebound forces. They are processed with high precision on CNC machine tools, resulting in high dimensional accuracy, low run out, and good balance, making the vehicle ride smooth and comfortable.
-
Enhanced safety with the use of magnesium alloy processed hubs:
The heat dissipation coefficient of magnesium alloy hubs is two to three times higher than that of ordinary hubs. Coupled with the structural characteristics of magnesium alloy hubs, the heat generated by the braking system is quickly conducted to the air. Even during continuous braking in long-term driving, the brake system can maintain a lower temperature, ensuring safe driving.
-
Improved aesthetics with the use of magnesium alloy processed hubs:
Magnesium alloy hubs have sophisticated exterior designs and diverse shapes that enhance the overall beauty of the vehicle. The design highlights the characteristics and exudes a sense of luxury and excellence.
-
Increased stability with the use of magnesium alloy processed hubs:
After using magnesium alloy processed hubs, the vehicle’s tires have improved traction, braking performance, and effective handling control, enhancing the driving experience.
-
Increased speed with the use of magnesium alloy hubs:
Using magnesium alloy cast and processed hubs helps effectively reduce the overall weight of the vehicle during operation, resulting in shorter acceleration times and higher driving speeds.
II. Manufacturing processes for magnesium alloy hubs:
-
Forging process for magnesium alloy hubs:
In the current traditional forging methods for magnesium alloy automotive hubs, the organization of magnesium alloy hubs still has issues of insufficient density and relatively low mechanical strength. To address these problems, technicians have developed an ideal forging method for magnesium alloy automotive hubs. This method significantly reduces the forging time, increases production efficiency, and produces magnesium alloy hubs with higher mechanical strength and density.
-
Casting process for magnesium alloy hubs:
Over the years, various casting techniques have been developed for magnesium alloy hub production, including precision forging forming technology, squeeze casting technology, low-pressure casting combined with squeeze casting technology, spin forging technology, semi-solid isotropic forming technology, squeeze casting combined with recasting technology, and vacuum tilt casting under differential pressure, etc.
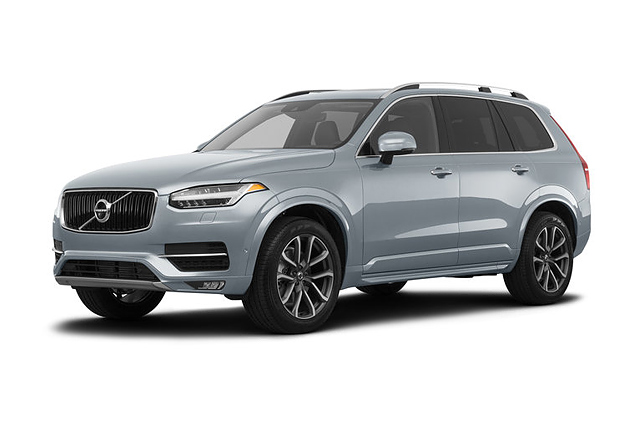
forged Magnesium (7)
-
Gravity casting process for magnesium alloy hubs:
In general, the gravity casting method uses a bottom-pouring pouring system and an externally attached tapered riser. Due to the difficulty in controlling the process, the related gravity casting processes may result in loose casting and insufficient mechanical properties and air tightness. When producing magnesium alloy hubs through gravity casting, the influence of alloy composition on performance and process should be analyzed first. Then, various measures should be taken to control the quality of the castings based on the effects of various process factors, achieving an efficient hub manufacturing process.
-
Pressure casting process for magnesium alloy hubs:
Vacuum pressure casting technology is a casting process that combines relevant vacuum extraction technology with the traditional pressure casting process. It realizes the removal or partial removal of gases inside the mold cavity, allowing the molten metal to fill the mold cavity under relatively vacuum conditions, and solidify under pressure. Magnesium alloy hubs produced by pressure casting have high dimensional precision and low surface roughness, among other excellent characteristics.
-
Low-pressure casting process for magnesium alloy hubs:
In general, the low-pressure casting method for alloy hubs is suitable for aluminum alloys. When using the low-pressure casting process for magnesium alloy hubs, there may be issues such as oxidation or combustion explosions. Therefore, low-pressure casting of magnesium alloy hubs becomes complex, and special attention should be paid to prevent oxidation during the process.
Magnesium alloy hubs are mainly used in the automotive and motorcycle industries. Currently, magnesium alloy hubs are relatively higher in price, which is related to their complex manufacturing processes. Achieving efficient casting of magnesium alloy hubs requires careful control of the manufacturing processes, selection of appropriate alloy compositions, and implementation of quality control measures. However, the advantages of using magnesium alloy hubs, such as improved comfort, enhanced safety, improved aesthetics, increased stability, and increased speed, make them an attractive option for light weighting and improving the performance of vehicles.