The reasons of Forged wheels are lighter as below.
Because the process method of forged wheels is to use high pressure (mostly several thousand tons of pressure) to press a piece of alloy that has been heated into a rough embryo (prototype) of the wheel, and then use CNC detail carving work for secondary processing, because it has withstood high pressure impact, so the molecules between the alloy will be smaller, the gap will be finer, the density will be higher, and the interaction force between the material molecules will be stronger, so the wheel only needs less raw materials to achieve Enough rigidity to make the overall weight lighter.
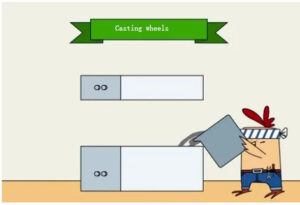
production of casting wheels
Forging is a production process that uses forging machinery to apply pressure to a metal billet to produce plastic deformation in order to obtain forgings with certain mechanical properties, shapes and sizes. In layman’s terms, forging is to heat the raw material to soften, and then obtain the final product after a thousand hammers.
In the casting method, aluminum is formed by changing the form of solid-liquid-solid. In contrast, forging is a process from “solid” to “solid”, which avoids the impurities and repeated changes in molecular structure that result in lower density, as well as the defects such as looseness and porosity that are difficult to avoid by the mold forming method. Therefore, compared with cast wheels, forged wheels have a tighter molecular structure, higher strength, smaller molecular gaps, and require less raw materials to achieve sufficient rigidity and lighter overall weight.
production of forged wheels
Aesthetics are a matter of opinion, but generally speaking, forged wheels have a higher degree of oxidation resistance and a longer lasting luster, allowing them to be shaped in a more simple and slender manner; cast wheels with a low degree of oxidation resistance are prone to yellowing and blackening, and will have visible pitting. When you knock on the wheel forging sound crisp, casting sound dull which is also very good to identify the difference.